The hidden causes of cost overruns in construction projects and how to manage them
- Last Updated : May 23, 2025
- 5 Views
- 4 Min Read
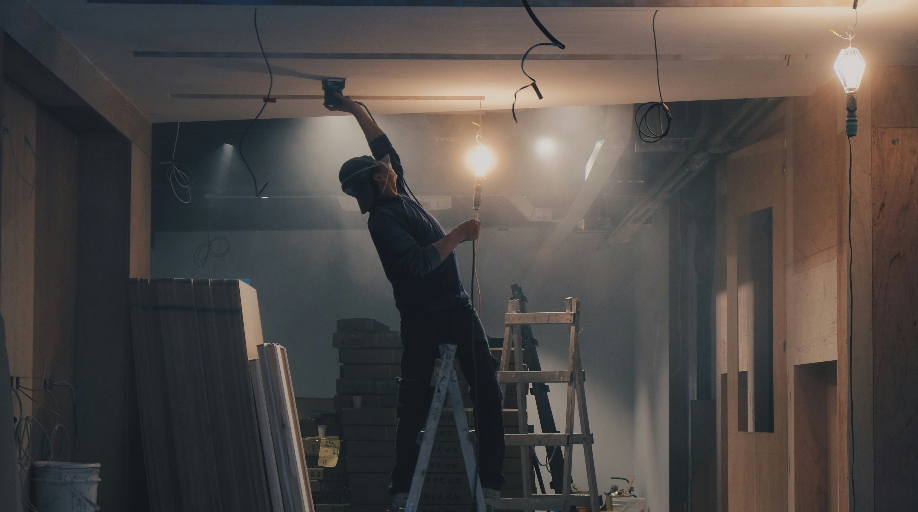
The construction industry has always played a big role in driving urban growth and supporting modern lifestyles. With more people moving to cities and a growing need for housing, the demand for construction services has continued to boom in recent years.
However, this growth doesn’t come without its challenges. With factors like environmental issues, labour shortages, and safety risks, a lot can get in the way of finishing a project on time, especially within a budget.
For businesses looking to grow, knowing what causes construction costs to rise—and how to avoid those problems—is essential to keeping projects on track and staying profitable. In this blog, we've listed some of the most common cost-related challenges that can happen during construction projects and ways to address them.
Poor initial project planning
One of the first and most crucial steps in kicking off any project is solid planning. As soon as you take on a client, you need a clear, structured plan for how you’re going to deliver the final result. That means everything from setting a budget to figuring out what resources you’ll need.
Any mistakes you make in estimating costs and timelines can lead to ripple effects that cause losses for both you and your client. To avoid this, the best approach is to have a dedicated expert or a team specialising specifically in project planning. The pre-construction phase should focus on assessing risks, conducting inspections on site, and gathering stakeholder input.
Allocate time for detailed design reviews and involve all key players (clients, consultants) early on to make sure you're all on the same page regarding scope and sequencing. The goal is not just to plan for the ideal scenario but also to anticipate potential issues and build in the ability to deal with contingencies.
Supply chain disruptions
As an industry that relies on multiple stakeholders working together, construction companies typically need to outsource certain tasks. However, there is a significant risk of disruptions if things don’t go as planned.
When it comes to critical aspects of a project, it's crucial to diversify your options and ensure that you have backup vendors in case one fails to deliver on time. Having contingency strategies in place can help you manage any potential complications.
Poor resource allocation
Another major issue in construction is poor organisation of resources. When your company is handling multiple projects, it's easy to under-staff a job site or face a shortage of materials during the project. This imbalance often leads to delays, missed deadlines, and increased labour costs—all of which significantly impact your profit margins. For instance, having too many workers on one site can result in idle time and unnecessary wage expenses, while too few workers on another can delay progress and outcome.
That’s why it’s essential to ensure that workers with the right skills are available at the right time and location. The best way to achieve this is by using a reliable project management system. For instance, with Zoho Projects, you can identify worker availability patterns across shifts and reassign resources based on evolving requirements. This helps avoid communication gaps, overworking, and under-utilisation of your workforce.
Uncertainty and budget overruns
Price fluctuations can have a major impact on profitability in construction. The price you quote to a client may change if material or labour costs rise unexpectedly. To avoid this, it’s important to include a buffer percentage in your budget to account for potential changes.
To protect both you and your client from sudden increases, it’s crucial to lock in prices early with vendors. This helps ensure you're not caught off guard by unexpected hikes. Another effective strategy is to purchase materials in bulk before prices rise. If the materials can be used across multiple projects, buying in larger quantities can help reduce overall costs and increase your profit margin.
Heavy reliance on manual processes
The construction industry has always depended heavily on manual labour. While that's understandable given the nature of the work, the industry has also seen significant advancements in machinery and technology over the years—not only at work sites but also on the business side. Yet, many construction managers have been hesitant to adopt these tools.
While not every business can afford expensive machinery, there are plenty of solutions that can help manage day-to-day operations without needing a massive investment. Being able to rely on your people is great—but manual processes often leave room for miscommunication and errors.
From keeping track of budgets to improving collaboration, project management tools can solve many of these challenges. For example, at Zoho, we offer a wide range of solutions for the construction industry: Zoho CRM for managing leads and tracking opportunities; Zoho Finance for budgeting, invoicing, and everything in between; Zoho Desk for handling queries quickly and efficiently; and much more.
Want to learn more? See how Zoho can help your construction business work smarter.
These are just a few of the many factors that can drive up construction costs—and some practical ways to manage them. Have you encountered any other cost-related challenges on your construction projects? Share your experiences in the comments below.